I. System Introduction Radio Frequency Identification (RFID) is a non-contact automatic identification technology that automatically identifies target objects and acquires relevant data through radio frequency signals. The identification work requires no human intervention. Compared with the synchronous or early contact recognition technology, it has non-contact identification (reading distance can be from 10cm to tens of meters), can recognize high-speed moving objects, resists harsh environment, has strong confidentiality, and can recognize multiple at the same time. It has outstanding features such as identifying objects, so it has a wider application field.
Typically, radio frequency identification systems consist of radio frequency tags and readers. A radio frequency tag is an electronic device that stores identifiable data in a radio frequency identification system. Generally, the radio frequency tag is installed on the recognized object, and stores related information of the recognized object as an electronic tag of the item to be identified. The information in the tag memory can be read/written by the reader. A reader is a device that reads information from a tag or writes information that the tag needs to store to the tag. The tag information read by the reader is managed and transmitted by the computer and the network system.
Radio Frequency Identification System Working Process: The RF energy is usually generated by a reader through a transmitting antenna in an area to form an electromagnetic field. The magnitude of the working distance depends on the transmitting power. When the tag passes through this area, an induced current is generated and energy is activated; the tag transmits information such as its own code through the built-in transmitting antenna, or overwrites the data stored in the tag according to the instruction of the reader. The reader receives the data sent from the tag, demodulates and decodes the received signal and then communicates with the computer network via a standard interface.
Distribution is an organizational part of the process of commodity circulation and an important part of logistics. In general, a distribution center is a modern distribution facility that engages in the provision of goods (collection, processing, distribution, picking, and distribution) and organization-to-user delivery to achieve high levels of sales and supply services.
The distribution center is developed based on the two needs of logistics rationalization and development of the market. It is a circulation-type logistics node that organizes distribution sales and supply and implements physical distribution as its main function. It is a good solution to the contradiction between the diversified needs of users and the mass production of specialized manufacturers. Therefore, it has gradually become the symbol of modern logistics.
Based on the deep understanding of the status and development trend of the domestic steel industry, the distribution center management system is based on the finished product business process model of the steel and metallurgical industry, introducing advanced radio frequency identification technology as a means to focus on improving the warehousing in the process. Monitoring and functions in storage, picking, processing, delivery, and transportation, reducing unnecessary links and losses in the process, improving the supply chain structure, and minimizing the cost of the circulation.
Using radio frequency identification technology and based on the principle of advancement and reliability, the system dynamically arranges and manages the business of transportation vehicle management, forklift management, pallet management, picking vehicle management and various shelf management to realize the operation process of the distribution center. The whole process of electronic operation, can establish a data interface with the customer service center to enable customers to achieve remote cargo management through the Internet. Through the Web-based system, the various data of the distribution center can be shared centrally at the headquarters. The headquarters management personnel can make timely and correct decisions and implement unified management of the distribution center business to improve operational efficiency, reduce the cost of each link, and ensure each The high speed operation of the link.
Second, the system is implemented
The basic operation process of this distribution center is shown in Figure 1:
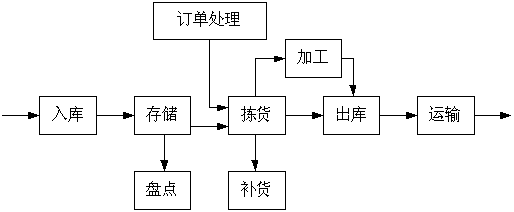
Figure 1 Distribution Center Basic Operation Process
Starting from the finished product line, after confirming the inbound goods through the “inbound†operation, the goods will be stored in storage in order. In order to ensure good protection and management of the goods in the warehouse, regular or irregular "counting" inspections are required. After receiving the customer's order, the order will be processed according to its nature, and then the customer's order will be taken out of the inventory area according to the processed order information, and the "picking" operation will be carried out. After the picking is completed, once it is found that the remaining stock in the picking area is too low, it must be "replenished" by the storage area or by reproduction. The goods to be processed are transported to the processing area for processing. After the sorted goods and the processed goods are sorted, they can be prepared for “outbound storageâ€. After all the delivery operations are completed, the driver can load the goods out of the delivery truck and “transport†them to each customer. goods.
The distribution of the distribution center is as follows: purchase area, storage area, delivery area, processing area, office area, logistics equipment storage area, as shown in Figure 2. Feeding area: The goods are received, weighed, bundled, and then put into the warehouse, and the relevant information of the goods is recorded into the computer or the back-end server. Storage area: Save the goods that will be shipped out. When picking the goods, pick the goods mainly from this area. Among them, it is divided into several cells, such as Area A and Area B. All use stereo storage. Processing area: After the picking is completed, the goods to be processed shall be transported to the processing area and processed according to the requirements of the customer. Delivery area: Put the goods after picking up or processed into suitable containers, ready for delivery and loading. Logistics equipment storage area: used to store handling equipment such as forklifts, trucks and picking vehicles and pallet storage equipment. Office area: Manage the operation process of the entire distribution center, and obtain the basic data of each link, and then upload the data to the headquarters data service center, and the headquarters management personnel can monitor the operation process in real time and make correct decisions based on the obtained data.
1. System hardware implementation plan and working principle (1) Storage The reader is installed at the entrance of the purchase area and the entrance of the inventory area. In the receiving area, the staff receives the goods. After the goods pass through the intelligent weighing system, the information about the weight is automatically transmitted to the data processing server in the office area, and the corresponding electronic label is printed. Among them, the label has already written information about the goods. For example, including: name, weight, batch number, serial number, ordering customer, production line, production date and other information. After the goods are bundled, the electronic label is affixed. When the forklift carries the pallet and the goods pass through the entrance of the purchase area, the reader automatically reads the information of the electronic label on the goods, transmits the information of the goods to the data processing server of the office area, forms a storage list, and displays on the front display. Display the name of the goods, the specific location on the shelf (ie the cargo) and other information. For example, the XX item is on the second floor of the C shelf of the cargo area B of the A cargo area. The forklift driver can place the goods according to the above information. The cargo warehousing model is shown in Figure 3.
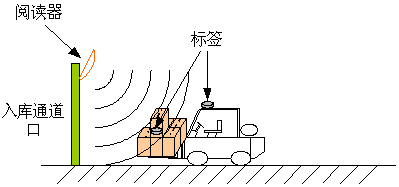
(2) Picking up the installation indicator light and the type display on the shelf where various goods are stored. When the office area enters the customer's goods order into the computer, the management software automatically generates the dispatched car list, and the storage position indicator and the variety display on the shelves of various goods will immediately display the selected goods and the required quantity, and the operator will The goods can be taken out of the shelf, put into the picking truck, and then the button is pressed, the position indicator light and the type display are extinguished, and then the operator goes to the next area to pick the goods until the picking work ends. The picking model is shown in Figure 4.
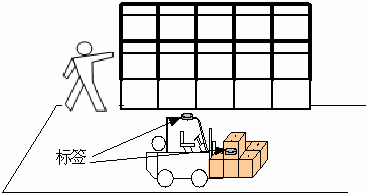
Figure 4 picking model
(3) Processing Install a reader and computer that can read and write on each processed product line. After the order is sorted, if the product needs to be processed, the picked product must be transported to the processing area for processing according to the customer's requirements. After processing, use the readable and writable reader to add information about the processing, such as specifications, size, weight, etc., to the label, and finally transport the processed goods to the shipping area for packaging and shipping.
(4) The library is installed at the exit of the storage area. When a picking truck or forklift loaded with goods passes through the storage area exit and enters the delivery area, the reader located above the exit automatically recognizes the tag data on the read goods and transmits the data to the data processing server in the office area. , compared with the original order, check processing, and then form a list of outbound.
(5) Cargo transportation Install electronic tags on the windshield of transport trucks; install readers, electronic truck scale intelligent weighing systems, gates, red and green lights and display screens at the gates. When the goods enter the delivery area, the goods are loaded into suitable containers or packaged for shipment. The information of the carried goods is written into the tag of the vehicle driver, for example, including the car number, the loading number, the name of the goods, the weight, the quantity, the destination, the route, the customer name, and the like. The driver placed the electronic tag on the windshield of the cab. When the vehicle arrives at the door post and passes the electronic truck scale intelligent weighing system, the data of the electronic tag in the cab interior is automatically read by the reader installed at the door whistle, and the weight information of the truck scale is automatically collected, The read tag information is transmitted to the data processing server of the office area, and then compared with the original data for verification processing. If it is correct, the display shows the car number, the loading number, the quantity, and the like, and the green light is on. The gate is opened and the vehicle is released, otherwise the red light is on and the gate is closed. The cargo transportation model is shown in Figure 5.
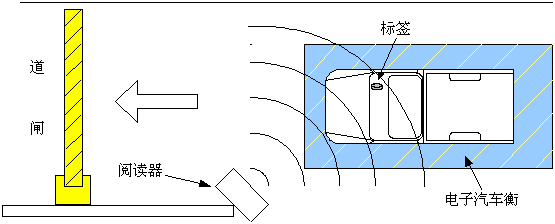
(6) Inventory In order to further determine that the actual quantity of stored goods is consistent with the data in the data processing server, it is necessary to perform inventory operations on the storage area periodically. Staff can use the handheld reader to collect information on a single piece of goods in the storage area. The collected data is transmitted to the data processing server through the wireless transmission device or the serial interface, and the library data is formed by the management software, automatically compared with the inbound data, and error processing is provided. In the storage area, the staff acquisition data model is shown in Figure 6.
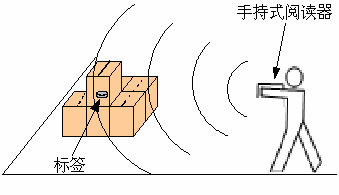
(7) Forklifts, pallets, trucks, picking vehicle management Install readers at the entrance and exit of the logistics equipment storage area; install electronic tags on forklifts, pallets, trucks, picking vehicles; in the storage area A reader is installed at the entrance and exit of each cell. When forklifts, pallets, trucks, and picking vehicles go out from the logistics equipment storage area, when the operations are performed in each cell in the storage area, the label information on them is automatically installed at the exits of the cells and the readers at the entrances. The data processing server of the office area monitors and schedules the device according to the received tag information, and displays the approximate location on the electronic map.
(8) Personnel management Writes relevant data information of the staff in the electronic tag and brings it to the staff. When the staff works back and forth in the distribution center, the electronic tag information of the person is automatically read by the reader installed in each area, and after the data processing server acquires the information, the staff running time and track are recorded, and the data is uploaded to the data management. Headquarters, used to generate a staff work assessment form.
2. System software implementation scheme The software system consists of the following subsystems: distribution center management system, transportation management information system, customer management information system, and basic data management system.
(1) The distribution center management system supports the management of the entire operation process in the distribution center area. The main functional modules include:
(1) Warehousing management: pre-entry planning inquiry, cargo pre-arrangement, receiving management, inspection management, warehousing planning, warehousing execution scheduling, and return management.
(2) Shipment management: pre-shipment plan inquiry, picking plan, picking execution scheduling, and outbound review.
(3) Inventory management: inventory adjustment, inventory management, finished product loss management, inventory control, and cargo classification management.
(4) Logistics equipment management: forklift, pallet, truck, picking vehicle dispatch management, status maintenance and inquiry.
(5) Inventory reserve analysis: inventory period analysis, safety stock warning, inventory ABC analysis.
(6) Inventory report: Inbound and outbound statements, daily statements.
(2) The transportation management information system can realize real-time dispatch management of own vehicles and cooperative vehicles as well as temporary vehicles, providing analysis of goods, calculation of loading, and selection of optimal transportation routes. Supports radio frequency identification systems and geographic graphics systems (GIS) for vehicle monitoring, dynamic tracking, vehicle scheduling, cost control and cycle accounting. And provide online vehicle and cargo tracking. The main functional modules include:
(1) Capacity management: Driver management fleet management: including own fleet management and agreement fleet management.
Capacity Management: View and maintain vehicle status.
(2) Transportation management / distribution management:
Transportation plan: Generate delivery route plan and vehicle delivery plan for the volume, weight and delivery address of the goods according to various delivery instructions.
Transportation dispatch management: transportation / distribution scheduling and maintenance. Combined with the GIS-based decision support system, it can realize capacity loading, vehicle scheduling and line optimization (including dynamic line management) for trunk transportation, distribution and transportation, and general cargo transportation.
Health problems, foster long-term loyal customer groups, and support the formation and integration of corporate supply chains. The main functional modules include:
(3) The basic data management system realizes efficient management of the basic data of the entire system by authorizing different management personnel with different management rights. The main functional modules include:
(1) General basic data: mainly classification, expense account, measurement unit, package type, status, customer or settlement object management, price management, etc.
(2) Organization and personnel management: organizational management, employee management, etc.
(3) System management: user management, system parameter management, role management, data backup, data recovery, etc.
3, system characteristics The system design concept is advanced, the application of advanced technology of radio frequency identification, and the reality is applicable. Its main features are as follows:
(1) Standardization and process management: It fully complies with the processing flow of steel enterprise distribution operations.
(2) Efficient performance of the task: using radio frequency identification technology to enable the system to efficiently store, inventory, pick,
Outbound management and forklifts, pallets, trucks, picking vehicle management, etc.
(3) The goods can be fully tracked and inquired according to the label of the product.
(4) The system has higher operating efficiency and lower system operating cost: the communication and communication time are greatly reduced, and the system access speed can be accelerated.
(5) System operation and data transmission security: The system strictly manages and records the operation user rights, and can track and monitor all operations. The data transmission process uses a strict security policy.
(6) Good scalability and recombinability: adapt to other business and development needs, and only need to write a new operation interface when the business is unchanged and a new operation mode is introduced. When business rules change, only minor modifications are required.
Oxygen Sensor For Subaru,Subaru Forester Oxygen Sensor,Subaru Oxygen Sensor,Subaru O2 Sensor
RUIAN XIANGTAI AUTOMOTIVE PARTS CO ., LTD , https://www.raxiangtais.com