Understand the mechanical structure of the machine tool: to understand the mechanical structure of the machine tool; to master the distribution of the machine tool's axis; but also to firmly grasp the positive and negative direction of the machine's various numerical control axes; to grasp the function and use of various parts of the machine tool, such as simple Pneumatic system principle and function, simple hydraulic system working principle and function; In addition to master the working principle and function of the auxiliary units of the machine tool, such as tool storage, cooling unit, voltage regulator, electrical cabinet cooler, etc. Principles, functions, and methods of use, as well as the working principle, function, and method of use of each safety door lock of the machine tool.
Firmly grasp the function of each operation button of the machine tool: know how to execute the program; how to check the machining state of the workpiece after suspending the program, resume the pause state and continue the program, how to stop the program; how to change the program and then execute the program, and so on.
Understand what kind of operating system your operating machine is; simply understand the control principle and working method of the CNC system; what kind of working language the system uses, the software used by the machine tool and the language it uses. If the operator does not understand the language or does not understand the professional vocabulary of the language, then professional training is required. Carefully take notes during the training. Each vocabulary in the machine tool represents what the Chinese language means and must be memorized. Back to master, then you can use the machine correctly in the future.
In addition, the operator also needs to learn and grasp the general operating alarm statement during training, and knows what Chinese means on behalf of it, how to solve the problem, and how to eliminate false alarms. In addition, for operators, if they have the energy and ability to do so, they can learn and master the language, which will greatly help to improve the machine operation skills in the future.
Secondly, it is necessary to master the manual or automatic operation of the control CNC machine tool and master the movement of each CNC axis that controls the machine tool.
The operator must achieve the realm of perfection and perfection, so that it can be done freely in any situation; only in the event of a collision or failure, the operator can correctly and timely deal with the problem, the operator will form a conditional reflex , decisively take braking measures.
In addition, the operator must be very familiar with the processing procedures of CNC machine tools; what kind of procedures and operations, the machine should have what kind of action, should be very familiar with. When the machine tool executes the program, you can know at the first time whether the machine action is correct and whether it needs to take braking measures. In addition, each beginner operator has more or less fear in the initial operation of the machine tool, fearing that the machine tool will hit a knife and collide with a machine. Then only after the operator has mastered the operation of the CNC machine tool, can he overcome similar fears. Third, he must master the program editing, parameter compensation of each process, and compensation for the diameter and length of the tool or grinding wheel.
First of all, after training, you must master the programming language, programming method and compensation method of each parameter you want to operate. Most advanced CNC machine tools are now equipped with a programmed or simulated PC workstation. So beginners can first perform software editing and machine cutting simulation learning on the workstation.
In the process of learning and programming, do not only pay attention to the simulation results. More importantly, you must learn the process of analog machining. You must understand what kind of tools or grinding wheels are used to process the workpiece. The machine tool CNC axis has completed the cutting process through the trajectory; When executing a specific process, the position and direction of movement of the relevant components in the machine tool; pay attention to the movement direction and cutting direction of each axis in the process of machining, including how to feed the tool, how to retract the tool, and pay attention to all the work in the machine tool processing. Step forward speed and displacement, the speed and displacement of the work in each step. In the simulation software for processing, note that all parameters must be entered correctly in the simulation process, do not sloppy input because of the simulation, so that the results of simulation processing may be incorrect; or cause subsequent collisions in the actual processing, or Parts are scrapped. If the simulation software has the function of anti-collision test, then use this function to check the correctness of the programming.
In addition, the operator needs to pay special attention to: simulation processing is only a theoretical result, does not mean that the machine will not collide in the actual cutting process, it does not mean that it can process qualified products. The purpose of simulation is to save programming time, improve the actual utilization of the machine tool, reduce the debugging time when processing the workpiece, and does not represent the actual part processing. Finishing the perfect workpiece machining is inseparable from the wisdom and sweat of CNC machine operators. Point four, the actual processing of the processing techniques, do a good job of preparation, first read the drawings, confirm the location of the workpiece to be processed, confirm the precision tolerances to be machined parts, and then edit the processing program. To prepare the workpieces, tools, or grinding wheels required for machining, prepare the inspection instruments needed in the machining process and prepare auxiliary tools and fixtures for the machining process.
When machining the first workpiece, the machine tool should use a single-step working state for trial cutting. When the machine program calls a new tool or grinding wheel, it should first perform tool setting to check whether the program action is correct.
When the workpiece is processed, it is necessary to adopt one clamping to complete the workpiece processing; if it is necessary to perform measurement or other reasons require the secondary clamping of the workpiece, then the positioning of the second clamping and the first clamping and the processing reference must be unified. . If the automatic positioning device of the machine tool is adopted, the measurement speed consistency of the automatic measuring system needs to be maintained. When the machining accuracy of the workpiece is detected, it can be completed on the machine tool, which can reduce the positioning error of the secondary clamping. In addition, when the precision of the dimensional tolerances of the machine tool is high in some parts of the machined workpiece, the operator needs to perform an accuracy check after each processing is completed, and then the workpiece is processed to the next position after the inspection; if the workpiece is The shape of a certain part is processed and synthesized in two or more directions. Then the machining in each direction will affect the positional or shape tolerance of the part shape. Therefore, the processing should be processed to have a small effect on the accuracy of the workpiece. Direction, and then processing the direction of higher workpiece tolerance requirements, and finally repeated processing, and finally approaching the required accuracy. If a standard measuring instrument is used on the machine tool, the workpiece cannot be measured, and the workpiece cannot be removed from the machine tool for measurement. Otherwise, the accuracy of the workpiece can be affected. Special gauges, plug gauges, gauges, etc. can be used. Detection, if the machine's own software with measurement capabilities, you can use the machine itself to measure the workpiece. After completing the processing of the entire workpiece, a full inspection of the workpiece is performed.
For the processing of batches of workpieces. When the initial program debugging is completed, then the machining program needs to be optimized. The basic principles of optimization are as follows: Prerequisites for ensuring machining quality, optimization of cutting parameters such as working speed, tool or grinding wheel rotation speed, infeed amount, machining depth, etc.; optimization of machining steps, optimization of machining standards, improvement of machining efficiency, use of high Life tool or grinding wheel to reduce the number of tool changes or the number of wheel corrections; establish a mathematical model of a reasonable machining program; edit an effective and reliable program; reasonably set the margin and number of rough finishes and use an appropriate forming tool or grinding wheel to increase efficiency , to ensure that the processing quality has a more significant effect.
To ensure the machining quality of the machined workpiece, attention should be paid to the following aspects: During the machining, the machine must be warmed up for a period of time to maintain the thermal balance of the machine axes during operation, and the temperature of the machined workpiece during the machining process should be kept as stable as possible. Work head, machine tool spindle, screw guides, scales, tool chucks or grinding wheel adapters for thermal and thermal balance. If the machine uses cooling oil and coolant, the temperature of the coolant must be kept constant. The temperature of the coolant is one of the important factors affecting the accuracy of the workpiece machining. The cooling system of the machine tool ensures the constant temperature of the coolant.
In general, factories need to be shut down at night, and the machine must be re-run the next day. Therefore, every day before the machine works, a heat engine is needed. In order to increase the utilization of the machine tool, there are two methods that can be used for machining. First, the original program is slightly modified after power-on, and a compensation amount far from the workpiece is made in all machining processes. In the machining process, the machine tool changes the correction value according to the measurement result when the machine tool is processed. After the machine tool is in thermal equilibrium, the correction is made. The value does not need to be changed. Another method is to process the part with a large workpiece tolerance at a certain time after starting up, and then wait for a certain period of time until the machine tool reaches thermal equilibrium, and then process the part with a higher tolerance in the workpiece; or use the machine first. After rough machining, after the machine tool reaches the thermal equilibrium, the workpiece is finished. For a workpiece with multiple datums, there are multiple dimensions that require higher accuracy. Then the workpiece should be machined with a reference that only defines one or two dimensions, but where the dimensional accuracy is more demanding, and where there are multiple dimensions for the same datum, the part with the highest precision should be machined first, and then the machining accuracy is higher. Low position. Because the machine tool is likely to produce waste when machining high-precision parts, the remaining parts of the workpiece can not be processed, thus saving processing costs. In short, the basic principles of processing: first roughing, removing the excess material of the workpiece, and then finishing; processing should avoid the occurrence of vibration; to avoid thermal deformation of the workpiece processing. The resulting vibrations occur for a number of reasons. They may be excessive loads, which may be the resonance of the machine tool and the workpiece, or may be due to insufficient rigidity of the machine tool, or may be caused by the passivation of the tool or grinding wheel. We can reduce vibrations by reducing the amount of infeed and machining depth, checking if the workpiece is clamped firmly, increasing the speed of the tool or reducing the speed to reduce the resonance, and see if there is a need to replace the new tool.
For beginners who operate CNC machines, collisions often occur. People often say that if you do not touch the machine tool, you will not learn to operate the machine. This is a very wrong and harmful understanding. Machine collisions are a great detriment to the precision of the machine tool, and the effects on different types of machine tools are also different. In general, the impact on the machine tool with less rigidity is greater, and for the machine tool with strong gantry structure, the impact is less under the same impact force. If the machine tool is cantilevered and the machine tool spindle is a machine tool structure mounted on a rotary axis, the impact on the accuracy of the machine tool can be fatal once the machine tool collides. So for high-precision CNC machine tools, the collision must be absolutely eliminated. As long as the operator carefully and masters a certain method of collision prevention, the collision can be completely prevented and avoided. The following points may help CNC machine tool beginners to prevent collisions.
The main reasons for the collision are: First, the wrong diameter and length of the tool or grinding wheel are input; the second is the input error of the workpiece size and other relevant geometric dimensions and the initial position of the workpiece is incorrectly positioned; the third is the workpiece coordinate system of the machine tool. The setting is wrong, or the machine zero is reset during machining and changes occur. Most machine collisions occur during the rapid movement of the machine tool. At this time, the impact of the collision is also the greatest and should be absolutely avoided. Therefore, the operator must pay special attention to the machine tool in the initial stage of the execution of the program and when the machine tool is changing the tool or grinding wheel. In this case, once the program is edited wrongly and the diameter and length of the tool or grinding wheel are entered incorrectly, it is easy to collide. At the end of the program, the sequence of retracting operations of the CNC axes is incorrect, and collisions may occur. In order to avoid the above-mentioned collision, when the cutter and the grinding wheel are used for the first time, it is necessary to carefully perform the alignment and the problem cannot be ignored. In order to avoid collisions, the operator must fully function in the operation of the machine tool to observe whether the machine tool has abnormal movements, whether there is sparks, whether there is noise and abnormal noise, whether there is vibration, and whether there is burnt smell. If abnormal conditions are found, the program should be stopped immediately. After the problem of the standby bed is resolved, the machine tool can continue to work. At the same time, before the operation, the operator should receive the safety training of the machine tool operation. Each type of machine tool should have a safe operation procedure. The operator should be trained in the operation and safety of the system, and only after they have a qualified induction card, can they work on the machine tool. Before working, you should know the location of the fire extinguisher, and the operator must master the method of the fire extinguisher, the position of the machine's air pressure switch, the position of the machine's input power switch, and the location of the hydraulic workstation, all of which are used to grasp the emergency shutdown method. The grinder for cooling oil should place the fire extinguisher within three meters of the machine.
In short, mastering the operating skills of CNC machine tools is a gradual process that cannot be accomplished overnight. It is based on mastering the basic operation of the machine, basic machining knowledge and basic programming knowledge. The operating skills of CNC machine tools are not static. It is an organic combination of imaginative and hands-on capabilities that requires the operator's components, and is innovative labor.
ESD Antistatic Fiber Glass FR4 G10 Sheet
ESD FR4 Sheet is a kind of anti-static materials which is added anti-static agents in the production of FR4 sheet, and effect FR4 to achieve the best anti-static performance. Substrate is an epoxy resin and fiberglass cloth.
Both surface and volume are 10^6--10^9. ESD FR4 sheet own flame redartant properties.
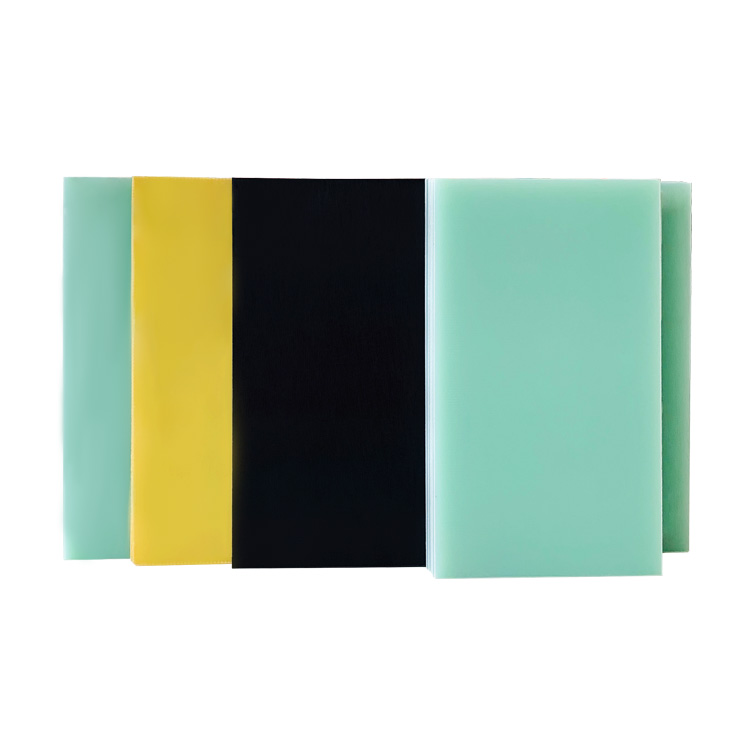
Feature:
1.Resistance value of ANTI STATIC BLACK FR4 is of 106~108Ω, and it has stable anti-static function. ANTI STATIC BLACK FR4 also has high mechanical strength, excellent processing performance and not easy to be affected by humidity and temperature.
2.ANTI STATIC BLACK FR4 is widely used in the construction of clean workshop (semiconductor, LCD, electronics, optics and medicine, etc.), clean room equipment shielding, space separation, clean equipment, observation window and equipment cover, electronic test fixture, etc.
3.Applicable industry of ANTI STATIC BLACK FR4: semiconductor industry, LCD industry, electronic and microelectronic equipment industry, electronic and electrical, communication manufacturing, precision instruments, optical manufacturing, pharmaceutical industry and biological engineering industries.
4.ANTI STATIC BLACK FR4 is divided into: total defense and surface defense
Name |
ESD Antistatic Epoxy Resin Sheet Fr4 Board |
Brand | HONY |
Color | Black |
Size | Thickness 0.8-80mm Width x Length 1020 x 1220mm |
Both surface and volume |
10^6--10^9 Ω |
Working temperature |
-10℃-170℃ |
ESD FR4 Characteristics
Extremely stable anti-static properties
Good mechanical strength
Good anti-static properties
Good intermediate electrical insulation
Non-conductive
Resistance to organic solvents
Working temperature up to 170 ℃
Good flame-retardant properties
ESD FR4 Application
Mobile phone test fixture, SMT technology countertops, PCB drilling
The semiconductor test fixture, semiconductor crystal manufacturing equipment parts
The wafer processing jig, sensitive electronic components, the hard disk drive means
The printed circuit boards, high-precision automated fixtures
Esd Fr4 Epoxy Fiber Glass,Fiberglass Composite Esd Fr4 Sheet,Anti-Static Esd Black Fr4 G10 Sheet,G10 Fr4 Esd Insulation Material
Hony Engineering Plastics Co.,Ltd. , https://www.honyplastic.com