The competitive landscape of the world's large-scale drying equipment manufacturing industry is changing, mainly reflected in the high concentration of manufacturers, the gap in the level of product technology is getting smaller and smaller, the user's personalized demand is outstanding, and the market demand changes from the quantity demand to the quality demand. Large drying equipment products have higher technical requirements. Since the beginning of the 1990s, some famous foreign large-scale manufacturers have transformed their doors, especially the large-scale drying equipment manufacturing industry in Germany, which was once the world's leading company. Due to the long-term recession of the world's drying equipment market, the world's large-scale drying equipment Competitors have been relatively weakened. The current situation in the domestic large-scale drying equipment industry can be said to be excellent.
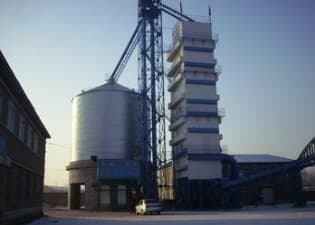
With the change in market demand, the domestic competitive landscape of the large-scale drying equipment industry has been broken. The number of manufacturers has grown from a few to dozens of manufacturers, and the level of product technology has developed rapidly. Compared with foreign products, the gap has become more and more. Small, the development of heavy-duty drying equipment industry in China has been highly valued by the world's peers. China's drying equipment is now basically flexible, composite processing, in the future to develop large-scale modular composite processing and drying equipment for the development direction, that is, the combination of two host machines into a composite processing and drying equipment, because the need for drying equipment to complete the processing The parts are mostly single-piece and small-batch, the process is complicated, the auxiliary time and the processing cycle are long, and all the processing steps are completed by one drying device, and the two combined machining centers can completely realize.
Energy conservation intensive route
After a long period of development, China's drying equipment has accumulated a certain amount of experience. When exploring the new development path of drying technology, comprehensive consideration must be given to energy efficiency, environmental protection, and product quality in order to achieve comprehensive, coordinated, and sustainable development. To implement the development strategy of high efficiency and green drying, we must first take the path of resource-saving development, and change the single extensive drying into a combination and intelligent drying. The development of dryers should also pay attention to energy saving and energy comprehensive utilization, such as adopting various joint heating methods, transplanting heat pump and heat pipe technology, developing solar dryers, etc., and developing automatic control technology of dryers to ensure optimal operating conditions. In addition, with the emphasis on environmental protection by human beings, improving the environmental protection measures of the drier to reduce the leakage of dust and exhaust gas will also be a need for in-depth research.
In the edible oil pressing plant, before the extrusion of oil from oil containing materials, an oil pretreatment process is typically undertaken to improve the efficiency of production and to ultimately save on costs. The entire oil milling process generally includes: cleaning, sieving, hulling, separation, cracking, particle making, frying, softening, flaking, drying, and expelling oil materials. The process: cleaner --> sheller --> huller --> crusher / flaker --> steam cooker --> softening --> extruder --> dryer.
Oil Pressing Plant Pretreatment
- Organic impurities, such as stems and leaves, cords and chemical fibers.
- Inorganic impurities such as soil and metal.
Advantages of Our Oil Pretreatment Technology
- Heated shelling features means to reduce energy consumption.
- Double dehulling process which raises the shelling ratio to up to 85% with oil residue in hulls reduced to below 1.5%.
- Large-volume silos to facilitate adjustments to production capacity.
- Can produce oil cake as different grades and various protein levels which are adjustable to meet special requirements. Soybean cake can also be milled.
- With years of research experience on screw Oil Press machine ,we can reach residual oil and low energy consumption.
- Complete pre-treatment system can be controlled automatically.
The Goal of Oil Pretreatment
- Improve the quality of the oil and the cake.
- Increase rate of productivity; reduce residual oil.
- Increase treatment capabilities of the equipment.
- Lessens wear and lengthens the life of the equipment.
- Ensures safety.
- Expansion improves the rate of productivity and the quality of the oil cake.
Oil Pretreatment Process
- Warm hulling process reduces energy consumption.
- Double cracking and hulling process improves the hulling ratio and reduce oil residue in the hull.
- High volume hull bin makes production flexible.
- Makes it possible to produce meals of various protein content (includes meal milling).
- Adopts the complete explosion puffing process.
- Automated controls.
Vegetable Oil Pressing Plant Turnkey Project
Cottonseed Vegetable Oil Pressing Plant Turnkey Project ,Soybean Oil Pressing Plant Turnkey Project ,Palm Oil Pressing Plant Turnkey Project ,Sunflower Oil Pressing Plant Turnkey Project
Dingzhou Yongsheng Grain & Oil Machinery Co.,Ltd. , http://www.oilpresschina.com